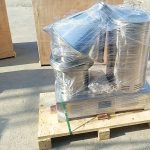
Shipping Peanut Butter Grinder Machine to Philippines
02/18/2025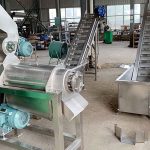
Industrial Juicer Machine FAQs
03/07/2025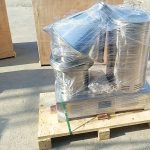
Shipping Peanut Butter Grinder Machine to Philippines
02/18/2025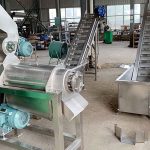
Industrial Juicer Machine FAQs
03/07/2025A colloid grinder is a vital piece of equipment for fine grinding and emulsifying materials in food, chemical, and pharmaceutical industries. However, due to the high-speed operation and friction between materials and grinding discs, excessive heat generation can become a concern. In practice, soybean milk produced by colloid mills typically reaches temperatures between 70-80°C. Similarly, grinding for peanut paste is around 70-75°C. Such high temperatures can affect product quality and reduce the lifespan of the equipment. In this post, we explore the common overheating problems in colloid mills, discuss practical solutions, and share Furui Machinery’s expert recommendations to ensure efficient and safe operation.
Common Overheating Issues
- Excessive Friction: High rotational speeds and rapid collisions between the grinding discs and the materials produce a significant amount of heat.
- Improper Operating Parameters: Fast feed rates and unoptimized grinding disc gaps can further contribute to overheating.
- Inefficient Cooling Systems: Without effective cooling- whether air, water, or oil - heat accumulates, compromising both product quality and equipment integrity.
- Material Challenges: High-viscosity materials and the presence of impurities increase the workload on the mill, leading to additional friction and heat generation.
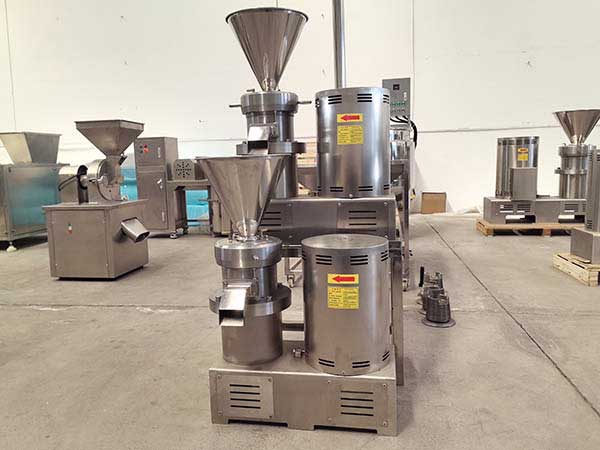
Colloid Mill
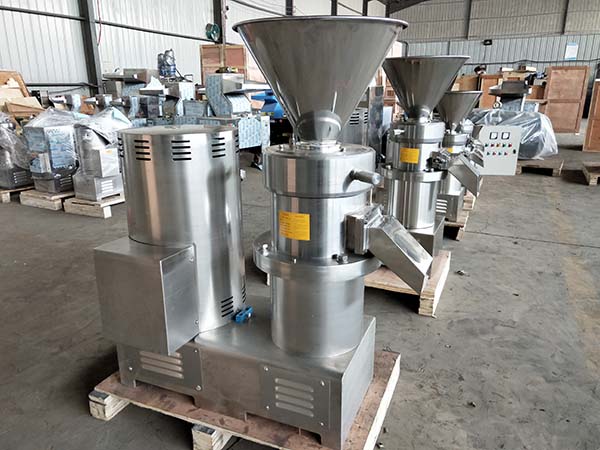
JMS-180 Colloid Mill
Solutions to Colloid Grinder Cooling
-
Adjust Equipment Operation Parameters
- Reduce Rotation Speed: Lowering the speed minimizes friction and collisions. Adjust the speed according to the material properties and mill model to balance grinding efficiency with temperature control.
- Control Feed Flow: A slower feed rate allows the material more time to grind and cool down, reducing the overall heat buildup.
-
Optimize Equipment Structure
- Enhance Cooling Systems: Equip the colloid mill with an efficient cooling system such as a circulating water system. Ensuring a steady flow of cooling water—or alternative coolants—can effectively dissipate heat. Consider increasing water flow or lowering its temperature to improve cooling efficiency.
- Adjust the Gap Between Rotor and Stator: Regularly check and adjust the gap between the rotor and stator. A well-calibrated gap ensures uniform grinding and minimizes unnecessary friction.
-
Improve Material Properties
- Reduce Viscosity: High-viscosity materials create extra load and friction. Modify the material composition or add appropriate diluents to lower the viscosity.
- Pre-Treat Materials: Remove impurities like metal particles or large contaminants before feeding the material into the mill. Also, crush the large materials into small sizes. This helps decrease friction and wear on the grinding surfaces.
-
Enhance the Working Environment
- Ensure Adequate Ventilation: Good airflow around the equipment helps disperse heat and any odors generated during operation.
- Avoid Direct Sunlight: Placing the colloid mill away from direct sunlight prevents additional heating from external sources.
-
Maintain Regular Equipment Care
- Clean and Lubricate Regularly: Regular cleaning and lubrication reduce internal friction and prevent wear, thereby controlling temperature and extending equipment life.
- Inspect Electrical Systems: Faulty electrical components can lead to excessive heat. Routine checks on motor and system connections are essential for maintaining optimal performance.
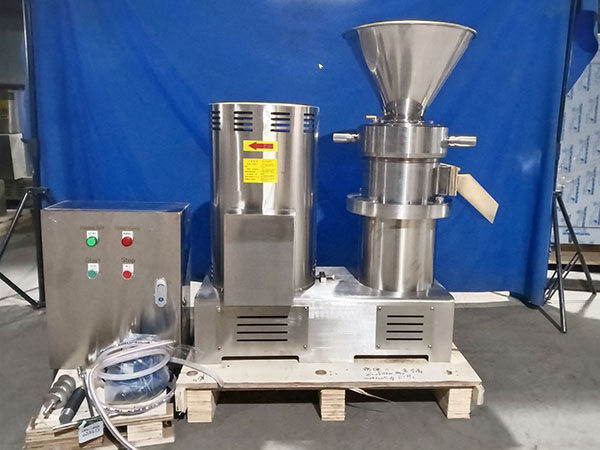
Colloid Mill to South Korea
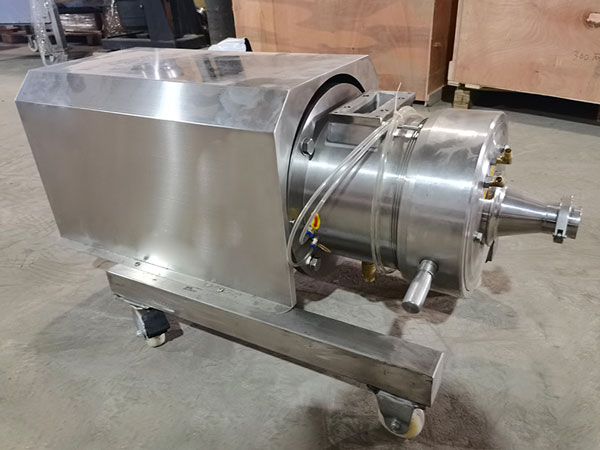
Horizontal Colloid Mill
Choosing the Right Cooling Method
Colloid mills typically use one of the following cooling methods:
- Air Cooling: Built-in fans expel hot air from the machine.
Ideal for small-scale operations or environments where water/oil cooling isn’t practical.
Low maintenance but less effective for heavy-duty, continuous use.
- Water Cooling: Uses an external water cycle to absorb and remove heat.
Requires a steady flow of water (10-30°C) to avoid thermal shock or condensation.
Best for high-intensity grinding applications.
- Oil Cooling: Circulates oil to dissipate heat, common in industrial-grade grinders.
Offers stable cooling but requires regular oil replacement to prevent contamination.
At Furui Machinery, our colloid machine is designed with:
- External Cooling Water Interfaces: Simplifying the integration of efficient water-cooling systems.
- Sealed Pressure Liquid Interfaces: Providing additional options for effective temperature management.
By incorporating these advanced features, Furui Machinery’s colloid mills help ensure stable operation, improved product quality, and longer equipment life.
How to Use Water Cooling Correctly
For water-cooled colloid grinders, follow these best practices:
- Keep water temperature between 10-30°C. Water that is too cold may negatively impact the grinding process or even cause equipment issues.
- Ensure consistent flow from inlet to outlet. The flow rate must be balanced --- not too slow to avoid insufficient cooling, and not too fast to compromise stability.
- Replace water regularly. Periodically replacing the water helps maintain optimal cooling performance and extends the life of the mill.
Conclusion
At Furui Machinery, we engineer our colloid mills with precision, integrating advanced cooling technologies. Our machines are built to deliver consistent performance, ensuring your processes remain efficient and your products meet the highest standards. Whether you’re grinding soybean milk, peanut paste, or processing high-viscosity materials, our colloid grinder is a perfect choice. If you have any questions or need more information on our colloid mills or cooling systems, feel free to contact us. We're here to help you achieve the best results for your production needs!